Metal 3D printing technologies have revolutionized the manufacturing industry, enabling the production of complex and customized metal parts with unprecedented ease. Among the various metal 3D printing technologies available, metal binder jetting, selective laser melting (SLM), electron beam melting (EBM) and direct metal laser sintering (DMLS) have emerged as the major players in the market. In this article, we will examine and compare these technologies based on several key factors to help you understand their strengths and applications.

Introduction
Metal 3D printing technologies have opened up a world of possibilities for engineers, designers and manufacturers. These technologies use different approaches to transform digital designs into physical metal objects, each with their own unique characteristics and benefits. Understanding the differences between these techniques will help you make informed decisions about which technology is best suited to your specific requirements.
Metal Binder Jetting
Metal Binder Jetting is a metal 3D printing technique that uses a powder-based approach. In this process, a thin layer of metal powder is spread on a build platform and a liquid binder is selectively sprayed onto the powder, bonding the particles together. The component is built up layer by layer until it is finished. It is then fused in a sintering furnace at high temperatures to form a solid metal part with excellent properties.
Metal Binder Jetting offers several advantages, including high productivity, lower material costs and the ability to print large parts. It is a versatile technology that supports a wide range of metals and alloys, including stainless steel, aluminum and titanium.
One of the key differences between metal binder jetting and other metal 3D printing techniques is that metal binder jetting does not require support structures. With many traditional 3D printing techniques, support structures must be created to support overhanging parts of the component during the printing process. These structures must then be removed in an often time-consuming post-processing step. With metal binder jetting, on the other hand, the surrounding unbound powder stabilizes the printed parts, eliminating the need for such support structures. This allows for greater design freedom while reducing post-processing time, resulting in more efficient and cost-effective production overall. However, the surface finish of metal binder jetting parts may require additional post-processing steps to achieve the desired quality.
A prominent manufacturer of metal binder jetting 3D printers is Desktop Metal

Selective laser melting (SLM)
Selective Laser Melting (SLM) is a powder bed fusion technique that uses a high-power laser to selectively melt and fuse metal powder particles together. The laser scans the powder bed according to design specifications and produces fully dense metal parts with excellent mechanical properties.
SLM is known for its high accuracy and resolution, enabling the production of intricate and detailed parts. It offers a wide range of material options that enable the production of parts with specific mechanical, thermal or chemical properties.
Another significant advantage of selective laser melting over other metal 3D printing technologies is its superior material density and strength. While other processes are often faced with voids and pores in the final product, SLM produces fully dense components with consistently high mechanical properties.

Despite all these advantages, selective laser melting (SLM) technology also has some disadvantages. Firstly, the cost of operating and maintaining an SLM machine is relatively high, as it requires both highly skilled personnel and expensive materials. Secondly, the process can be time-consuming, especially for large and complicated parts. In addition, the final products can often require post-processing to reduce surface roughness or improve accuracy of fit.
Electron beam melting (EBM)
Electron beam melting (EBM) is another powder bed fusion technique that uses an electron beam instead of a laser to melt and fuse metal powder. EBM offers faster build speeds and better material utilization compared to SLM. It is particularly suitable for the production of large, intricate parts. EBM uses a high vacuum environment to ensure accurate melting of the metal powder. Although there can be some limitations in terms of surface finish and resolution, EBM excels at producing parts with good mechanical properties and can be cost-effective for certain applications.
Despite the many advantages, electron beam melting (EBM) also has some disadvantages. The high vacuum environment required for EBM is expensive to purchase and maintain. In addition, the need to carefully clean and maintain the machine after each use can affect production speed. The surface finish of the parts produced can be rougher than with other methods, which may require reworking. In addition, the resolution of EBM can be limited compared to other methods such as selective laser melting (SLM). This can mean that smaller, more detailed components cannot be produced as accurately. Finally, the energy efficiency of EBM can be lower as more energy is required to maintain the high vacuum environment and generate the electron beam, which can increase the cost of part production.

Direct metal laser sintering (DMLS)
Direct Metal Laser Sintering (DMLS) , also known as laser powder bed fusion, is a metal 3D printing technique that uses a laser to selectively fuse metal powder particles together. DMLS is capable of producing highly complex, fully dense metal parts with excellent mechanical properties.
DMLS offers a wide range of material options, enabling the production of parts with specific material properties. It can achieve fine details and intricate geometries, making it suitable for applications that require high precision and design complexity. However, DMLS can have limitations in terms of build speed and scalability.
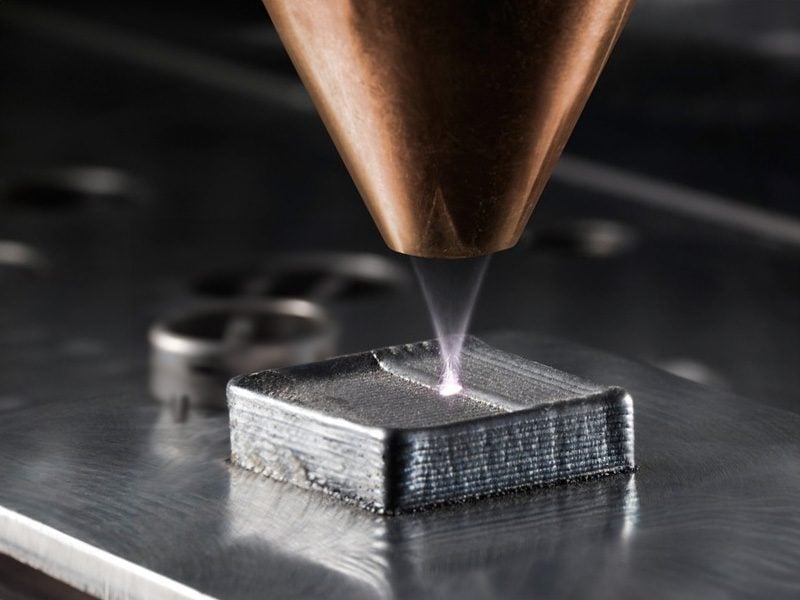
Although Direct Metal Laser Sintering (DMLS) offers many remarkable advantages, it also has some disadvantages. One major disadvantage is the high cost. Both the purchase of DMLS machines and their operation and maintenance can be a significant expense. In addition, the metal powder required for the process is usually quite expensive. Another disadvantage is the speed of the construction process. Compared to other 3D printing technologies, DMLS can be slower as each layer of metal powder is individually fused by a laser. This time-consuming process can increase production times and is therefore less suitable for high-volume production or when quick turnarounds are required.
Comparison factors
A thorough comparison of different metal 3D printing technologies requires comprehensive consideration of a variety of factors. It is important to highlight all relevant aspects in order to make an informed decision. In the following, these factors are explained in detail to provide a comprehensive understanding of the differences and special features of each technology.
Material options
Each technology has its own compatible materials. Metal Binder Jetting supports a variety of metals and alloys, including stainless steel, aluminum and titanium. SLM, EBM and DMLS also offer a variety of material options that enable the production of parts with specific mechanical, thermal or chemical properties. It is worth clarifying in advance exactly which materials you want to use.
Surface finishing and post-processing
The surface finish of 3D-printed metal parts can vary depending on the technology used. Metal binder jetting may require additional post-processing steps to achieve the desired surface quality. SLM and DMLS typically produce parts with smoother surfaces, while EBM may require additional surface treatments.
Accuracy and resolution
Accuracy and resolution play a crucial role, especially in the production of intricate or highly detailed parts. SLM and DMLS are known for their high accuracy and resolution, enabling the creation of complex geometries with fine details. Metal Binder Jetting and EBM have a slightly lower resolution, but can still achieve satisfactory results for many applications.
Build speed and scalability
Build speed and scalability are important aspects, especially for large-scale production. Metal Binder Jetting is known for its high productivity and scalability and is therefore suitable for manufacturing applications. SLM and DMLS offer good build speeds, but can be slower compared to Metal Binder Jetting. EBM is characterized by a relatively high build speed and is often preferred for large, complex parts.
Cost considerations
Cost considerations play an important role in the adoption of metal 3D printing technologies. Metal Binder Jetting generally offers lower material costs and higher productivity, making it a cost-effective option for certain applications. SLM, EBM and DMLS may have higher equipment and material costs, but still offer excellent quality and versatility.
Applications
Metal 3D printing technologies are used in various industries, including aerospace, automotive, medical and jewelry. The cost-effectiveness and scalability of metal binder jetting make it ideal for rapid prototyping and low-volume production. SLM, EBM and DMLS are commonly used for the production of functional prototypes, complex components and customized medical implants.
Conclusion
Metal 3D printing technologies have revolutionized the way we design and manufacture metal parts. Metal binder jetting, selective laser melting, electron beam melting and direct metal laser sintering offer unique advantages and possibilities. Choosing the right technology depends on specific requirements such as material properties, surface finish, accuracy, build speed, scalability and cost considerations. By understanding these factors, you can harness the power of metal 3D printing to drive innovation and transform your manufacturing processes.
Frequently asked questions
- What is the difference between Metal Binder Jetting and other metal 3D printing technologies?
Metal Binder Jetting uses a powder-based approach with a liquid binder, while other technologies such as SLM, EBM and DMLS use a laser or electron beam to selectively melt metal powder particles. - Which metal 3D printing technology offers the highest accuracy and resolution?
Among metal 3D printing technologies, Selective Laser Melting (SLM) and Direct Metal Laser Sintering (DMLS) are considered to have the highest accuracy and resolution. These technologies enable the creation of metal parts with exceptional precision and fine detail. Both SLM and DMLS use a laser to selectively melt metal powder and build it up layer by layer into a three-dimensional object. These precise laser processes enable the production of complex geometries with high accuracy and sharp edges. Thanks to the fine layer resolution, even small details and intricate structures can be realized with great precision. The high accuracy and resolution of SLM and DMLS make them particularly suitable for applications where tight tolerances and sophisticated surface details are required, such as in the field of functional prototypes, aerospace or medical technology. However, it should be noted that the actual accuracy and resolution may also depend on other factors such as the material composition used and the process parameters. - Which metal 3D printing technology is the fastest and most suitable for series production?
Among the various metal 3D printing technologies, metal binder jetting is considered one of the fastest options and is particularly suitable for series production. This technology is characterized by high productivity and scalability, which means that it is capable of producing large quantities in a short time. Metal Binder Jetting enables the simultaneous production of several parts, resulting in efficient series production. Due to the fast build speed of the process, companies can shorten production times and thus optimize their delivery times. In addition, Metal Binder Jetting offers the ability to produce complex geometries and thin-walled structures with high precision, making it an attractive choice for series production of metal parts. However, it is important to note that the selection of the optimal technology for series production also depends on other factors such as the specific requirements of the project, the desired material properties and cost considerations. - Which industries can benefit from metal 3D printing technologies?
Regardless of the industry, companies can benefit from the possibilities of metal 3D printing, whether by accelerating prototyping and manufacturing processes, producing individualized products or realizing sophisticated design concepts. Metal 3D printing has the potential to fundamentally change the way we develop and manufacture products, making it a valuable technology for companies in a wide range of industries. - Are there limitations to using metal 3D printing technologies?
Each technology has its own limitations, such as material options, surface finish, build speed, scalability and cost considerations. Understanding these limitations is critical to selecting the most appropriate technology for a given application.
Sources:
https://de.wikipedia.org/wiki/Binder_Jetting
https://de.wikipedia.org/wiki/Selektives_Laserschmelzen
https://de.wikipedia.org/wiki/Selektives_Elektronenstrahlschmelzen
https://de.wikipedia.org/wiki/Selektives_Lasersintern