Desktop Metal Shop System
A revolutionary solution for the series production of metal parts
The Desktop Metal Shop System is the world's first metal binder jetting system designed specifically for series production. It revolutionizes the production of metal parts with its high printing speed, outstanding print quality and impressive productivity. With its ability to support a wide range of materials, the Shop System offers a versatile and cost-effective solution for modern workshops. The Shop System consists of four main components: a 3D printer, a drying oven, a powder station and a sintering oven. These components work seamlessly together to enable efficient and effortless printing of end-use parts.
High productivity
The Shop System enables fast and efficient production of metal parts. With its advanced metal binder jetting technology and high printing speed, you can produce more parts in less time, increasing your productivity.
Cost efficiency
The Desktop Metal Shop System offers a cost-effective solution for the series production of metal parts. By using metal powder and optimizing the use of the material, you can save on material costs. In addition, the efficient design of the system enables a reduction in post-processing time and costs.
Design freedom
With the Shop System, you can print complex geometries and intricate structures that are difficult or impossible to realize with conventional manufacturing methods. This opens up new possibilities for the design of metal parts and enables you to develop innovative and unique products.
Versatility
The store system supports a variety of metal materials, including stainless steel, aluminum, titanium and special alloys. This allows you to select the appropriate materials for your specific applications and cover a wide range of industries.
Sustainability
Thanks to the possibility of powder recycling and the efficient use of materials, the store system contributes to the reduction of material waste and sustainable production. It enables you to implement more environmentally friendly production processes and make a contribution to the circular economy.
Flexibility
The store system offers you flexibility in series production. Thanks to the options for large build volumes, you can adjust the production capacity as required and process both small and large quantities efficiently.
Components of the Desktop Metal Shop System
3D printers
The Metal Binder Jetting (BJ) 3D printer is the heart of the store system. It enables the fast and precise printing of high-resolution metal parts. With its advanced technology and versatile application options, the 3D printer is an essential part of the Shop System.
Learn more
Build sizes | 350 x 220 x 200 mm 350 x 220 x 150 mm 350 x 220 x 100 mm 350 x 220 x 50 mm |
Resolution | 1600 x 1600 DPI |
Footprint | 199.4 x 76.2 x 162.6 cm (78.5 x 30 x 64 in) |

Drying oven
After printing, the component chamber with the printed parts is placed in a cross-linking oven. Cross-linking is a thermal curing process that gives the green parts additional strength before they are de-powdered.
Learn more
Dimensions (H x W x D) | 1100 x 910 x 740 mm (43.3 x 35.8 x 29.1 in) |
Weight (without powder) | 110 kg (243 lb) |
Power requirement | 230 VAC, 50/60 Hz, 17.5 A, 2.97 kW |
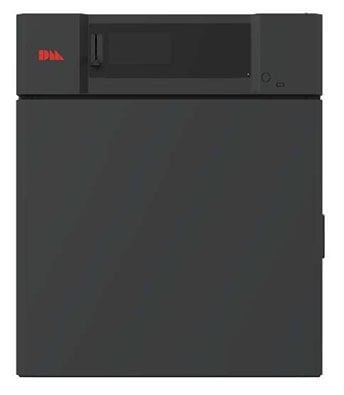
Powder station
The powder station is a central component of the store system. It enables efficient and safe handling of the metal powder. The station removes excess powder from the printed parts and recycles it for the next print run. This ensures optimum use of the material and contributes to cost savings.
Learn more
Powder management | Built in powder recovery and sieving Controlled metering |
Sieving rate | 5 kg/hr |
Footprint | 101.6 x 68.6 x 162.6 cm (40 x 27 x 64.0 in) |

Sintering furnace
The sintering furnace in the Shop System is responsible for sintering the printed parts. In this step, the parts are heated to high temperatures to remove the binder and compact the metal powder into a durable metal part. The furnace ensures precise and reliable sintering and guarantees the quality of the end products.
Learn more
Gas | External gas hookup |
Peak temp | 1400 °C |
Footprint | 161.8 x 138.0 x 75.4 cm (63.7 x 54.3 x 29.7 in) |

Printing process
The printing process with the Desktop Metal Shop System consists of three steps. These enable the efficient production of high-quality metal parts with complex geometries and excellent mechanical properties. The process is precise, reliable and offers high reproducibility of the printed parts.
- Printing: For each layer, the printer spreads metal powder on the print bed and precisely injects a binder to bind the loose powder and define the geometry of the part. Layer after layer of metal powder and binder is applied until the entire build volume is filled with bonded parts and the surrounding loose powder.
- De-powdering: Once a print has been completed and cured in the drying oven, the print build is removed and taken to a powder station to remove excess and fine powder. This is done using a suitable powder removal tool, such as a brush or compressed air. The excess powder is removed from the parts and recovered by an integrated powder recycling system with powder sieving.
- Sintering: The de-powdered parts are then sintered in a furnace. Here, the parts are heated to high temperatures to remove the binder and compact the metal powder. The furnace ensures precise sintering and transforms the printed parts into solid metal parts with high density and strength.
Advantages
Easy to use and operate
The Desktop Metal Shop System was developed specifically for modern machine shops and fits seamlessly into your workflow. It enables you to produce parts with outstanding surface finish and resolution at a fraction of the cost of laser-based 3D printing systems.
Affordable & turnkey

The Desktop Metal Shop System provides all the equipment your machine shop needs to get started with binder jetting - from printing to sintering. It is available in various build volume configurations (4L, 8L, 12L and 16L) and has been specifically designed to match the throughput of your shop.
Simple sintering with Live Sinter™

Take the guesswork out of sintering printed parts. Live Sinter solves the decades-old problem of part shrinkage and deformation through predictive counter-deformation. The software simulates the complex forces parts are subjected to during sintering and automatically adjusts geometries to achieve the desired dimensions after printing according to the original, intended design specifications.
Simplified post-processing
The parts printed on the Shop System™ are fully supported in the powder bed and are equipped with manually removable sintering devices. This eliminates the time-consuming processing of support structures that is common with laser-based 3D printing systems. Instead, you get near-finished parts straight from the oven.
Unparalleled productivity
Boost your company's performance by using 3D printing. With ease, you can print end-use metal parts that have the quality, surface finish and tolerances required to fit seamlessly into machining operations.
10x faster than other metal 3D printing systems
The Desktop Metal Shop System uses a high-speed printing system that can produce high-quality metal parts in a single pass. Compared to laser powder bed fusion systems, it allows up to 10 times the speed. This means you can print hundreds or even thousands of metal parts per day.
One finished print per work shift
Average cycle times of 6-12 hours allow new parts to be produced every shift. With the ability to print dozens to hundreds of near-finished parts every day, you can reserve machine operators' time for refining key features.
Working with flexible batch jobs
The Shop System™ offers a tool-free production process. At the touch of a button, you can seamlessly switch to a new job and process multiple complex jobs without the need for individual set-up.
Superior print quality
Print customer-ready parts with high resolution and impressively fine details. With the Desktop Metal Shop System, you can achieve surface finishes of up to 4 µm Ra directly after sintering. It produces dense and solid parts that require no debinding or filling.
High-resolution metal 3D printing
The Desktop Metal Shop System offers the highest resolution single-pass binder jetting system on the market today. With a native resolution of 1600×1600 DPI (a 33% higher resolution than comparable systems) and over 670 million drops per second, the Shop System™ delivers high-resolution 3D printing at high speed.
No compromises thanks to adaptive printing system

Users of the Shop System™ do not have to compromise on detail or resolution in the name of speed. With a droplet size of 1.2 pL and automatic droplet multiplexing of up to 6 pL, the Shop System™ achieves outstanding surface finish, precise gate control and high detail at high speed.
Reliability: 5-fold print redundancy
Users of the Shop System do not have to compromise on detail or resolution in the name of speed. With a droplet size of 1.2 pL and automatic droplet multiplexing of up to 6 pL, the Shop System™ achieves outstanding surface finish, precise gate control and high detail at high speed.
Print examples
Use these examples to get an idea of how many parts you can print and at what cost with the Desktop Metal Shop System.
Download
Brochure Desktop Metal Shop System
CONTACT
Our experts will be happy to help you. Get in touch with us!